Note: The PCON-CA / CFA Field Network Controllers has been moved to the Obsolete Products Archive.
Replacement models are listed in the Notice for Discontinuation of PCON-CA / CFA - October 2021
Cleanroom Type added!
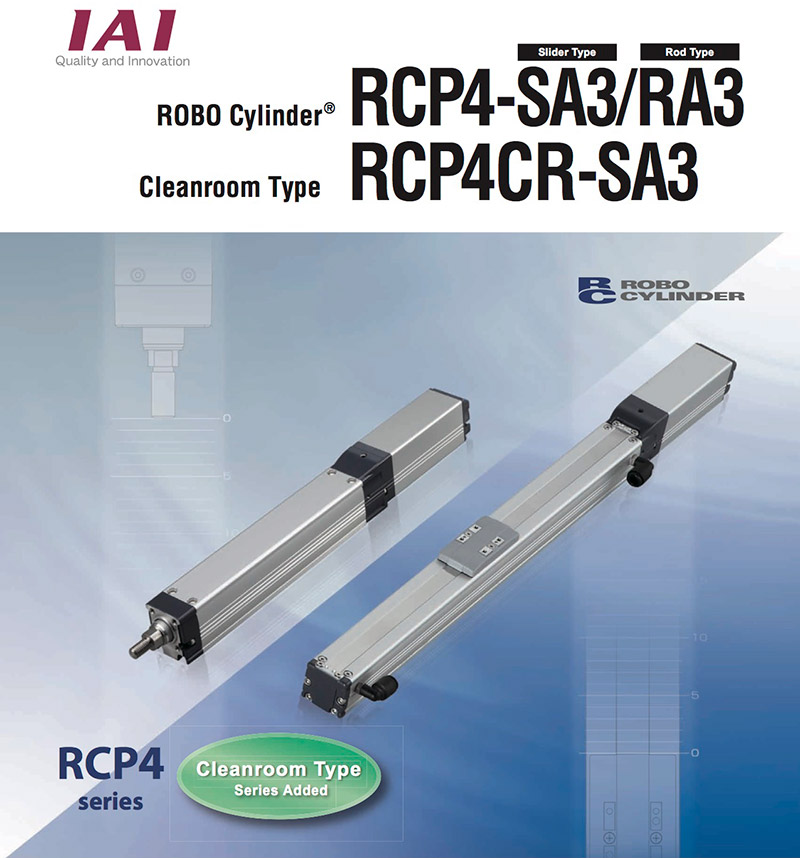
RCP4-SA3/RA3
Catalog #: CE0220-3A-1215
Pages: 16
File size: 3.2MB
SA3/RA3 Type with 32mm Actuator Width Now Has a Side-mounted Motor Type:
* RCP4-SA3R – Side-mounted Motor, Slider Type
* RCP4-RA3R – Side-mounted Motor, Radial Cylinder Rod Type
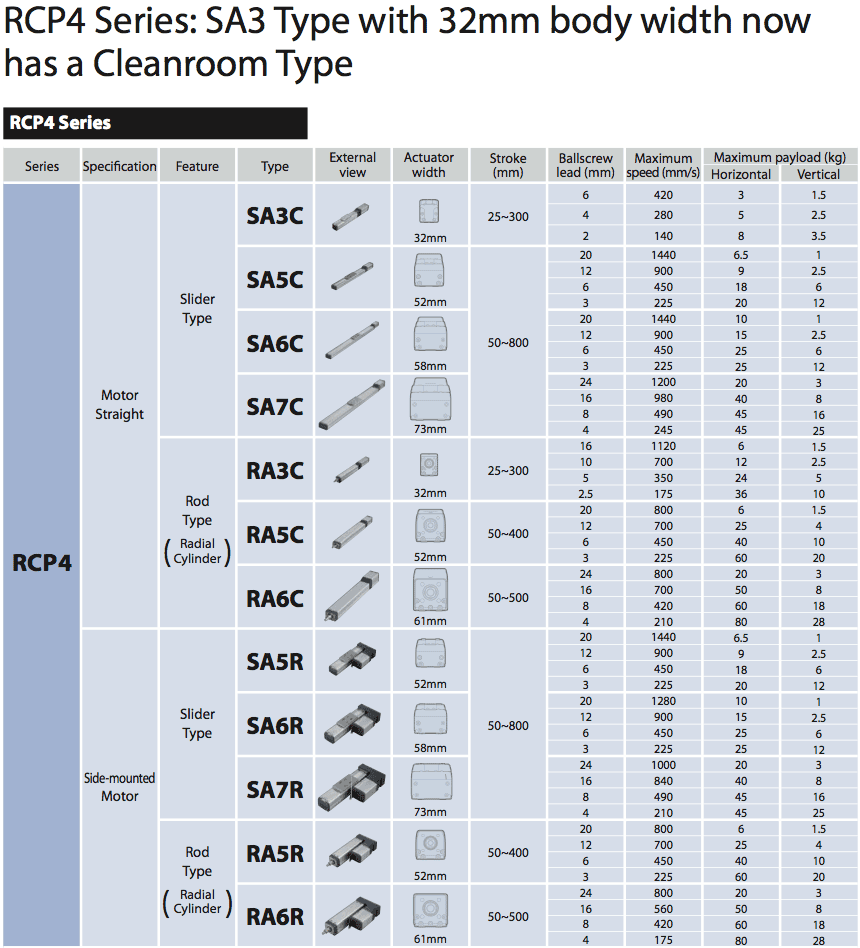
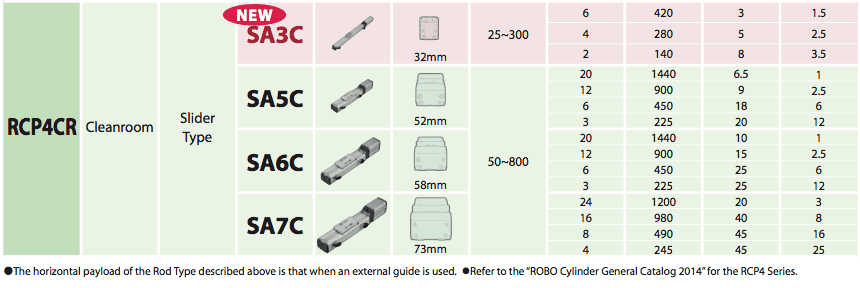
1.5 Times the Speed and Double the Payload
The Power CON 150 series boosts the performance of ROBO Cylinder® standard motorized cylinders to amazing new heights. Introducing the PCON-CA model combining a Power CON 150 controller with a RCP4 actuator supporting the new high-output driver.
RCP4 Series Variations
Type | Model | Width | Stroke | Ball screw lead (mm) |
Maximum speed (mm/s) |
Maximum payload (kg) | Maximum acceleration |
|
Horizontal | Vertical | |||||||
Slider | SA5 | 52mm | 50mm ~ 800mm | 20 | 1440 | 6.5 | 1 | 1G |
12 | 900 | 9 | 2.5 | |||||
6 | 450 | 18 | 6 | |||||
3 | 225 | 20 | 12 | |||||
SA6 | 58mm | 50mm ~ 800mm | 20 | 1440 | 10 | 1 | 1G | |
12 | 900 | 15 | 2.5 | |||||
6 | 450 | 25 | 6 | |||||
3 | 225 | 25 | 12 | |||||
SA7 | 73mm | 50mm ~ 800mm | 24 | 1200 | 20 | 3 | 1G | |
16 | 980 | 40 | 8 | |||||
8 | 490 | 45 | 16 | |||||
4 | 245 | 45 | 25 | |||||
Rod | RA5 | 52mm | 50mm ~ 400mm | 20 | 800 | 6 | 1.5 | 1G |
12 | 700 | 25 | 4 | |||||
6 | 450 | 40 | 10 | |||||
3 | 225 | 60 | 20 | |||||
RA6 | 61mm | 50mm ~ 500mm | 24 | 800 | 20 | 3 | 1G | |
16 | 700 | 50 | 8 | |||||
8 | 420 | 60 | 18 | |||||
4 | 210 | 80 | 28 |
Controller
Series | Model |
PCON | CA |
Shorter Takt Time Significantly Boosts
the Productivity of Your System
New Functions of the RCP4 Actuator

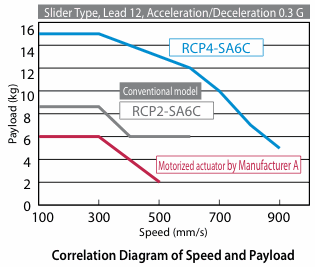
(*) The specific rates of improvement vary depending on the model.

From the current RCP2 series, we selected three slider types (SA5/SA6/SA7) and two rod types (RA5/RA6), which are among the most widely used actuators. We plan to add more variations in the future.
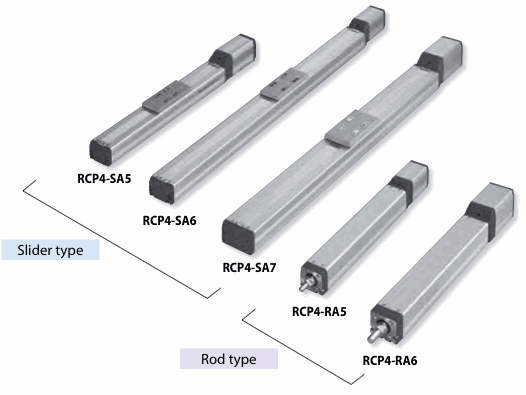

The rod type
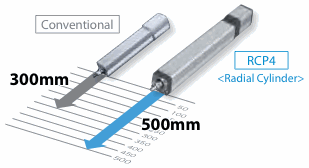
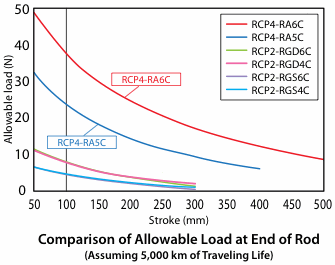

The motor has been unitized for easy replacement. The actuator and motor unit can be separated and replaced by removing only one setscrew, so the time required for maintenance becomes significantly shorter.
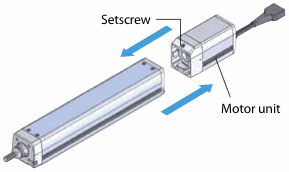

Slider types have mounting holes that are compatible with RCP2 actuators, meaning that you can replace your current RCP2 actuator with a RCP4 with ease. Also, the mounting holes provided on rod types are the same as those provided on slider types, instead of T-slots found on the RCP2, and reamed holes are also provided to significantly improve installation repeatability.
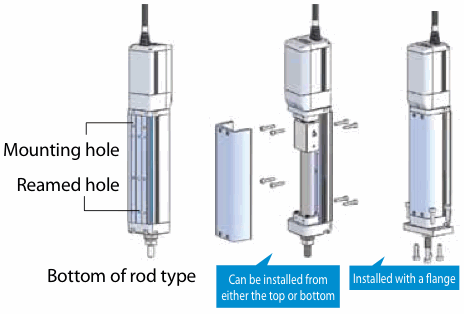
New Functions of Power CON 150 PCON-CA

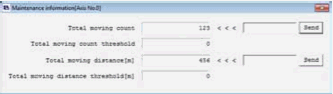

The total distance travelled by the actuator is counted and recorded in the controller, and a signal is output to an external device once the pre-defined count is exceeded. By using this function, you know when to add grease or perform periodic maintenance.

The calendar function (clock function) lets you add timestamps to the history of alarms, etc. This information is useful in troubleshooting, etc.
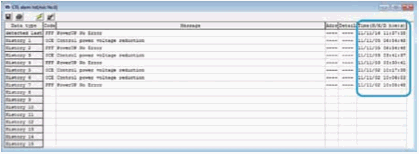
Takt Time Minimizing Function

The takt time minimization function is a new feature added to the ROBO Cylinder PC software (Ver. 8.03.00.00 or later) and touch-panel teaching (model number CON-PTA). All you need is to connect the actuator to a controller supporting this function and enter the actuator model, load, etc., and optimal acceleration/deceleration and speed according to the load will be set automatically.
The first step to using the takt time minimization function is to set the model number of the actuator used and the load (mass) to be transported.
1. Setting the acceleration/deceleration from the speed
Enter a desired speed in the position data table, and the maximum settable acceleration/deceleration will be set automatically according to the pre-defined load-speed combinations.
2. Setting the acceleration/deceleration and speed from the travel
Specify the position data number associated with desired start/end positions of movement and set a desired travel distance, and the combination of acceleration/deceleration and speed that gives the shortest travel time will be set automatically.
You can select a controller of one of two types: the positioner type where position numbers are specified by I/Os (input/output signals) from a PLC, etc., and the pulse-train type where the actuator is directly operated by sending pulses from a positioning unit. (Pulse-train controllers also support positioner operation using I/Os.)
Typical operating noises of pulse motors are reduced at low speed.
Do you have any questions or comments about our products? Contact Us.